Spritzguss
Der Spritzguss ist ein unverzichtbares Verfahren für die industrielle Massenproduktion von Kunststoffteilen. Er besticht durch Präzision und Vielseitigkeit – mit dem Spritzgussverfahren lassen sich nahezu beliebige Formen und komplexe Geometrien herstellen. Somit ist der Spritzguss in vielen Branchen die bevorzugte Methode zur Herstellung hochwertiger und langlebiger Kunststoffteile.
Spritzguss ist effizient und präzise. Diese Verfahrenstechnologie in der Kunststoffverarbeitung ermöglicht es, große Stückzahlen in gleichbleibend hoher Qualität herzustellen. Komplexe Formen und spezielle Materialeigenschaften lassen sich vielfältig realisieren. Diese Faktoren machen den Spritzguss zu einem wirtschaftlichen und flexiblen Verfahren für eine Vielzahl von Anwendungen. Die Flexibilität des Verfahrens ermöglicht den Einsatz in nahezu jedem Bereich, der auf präzise gefertigte Kunststoffteile angewiesen ist. Insbesondere bei hohen Stückzahlen überzeugt die Wirtschaftlichkeit von Spritzguss.
Vom kleinen bis zum großen Kunststoffteil erfüllt Spritzgießen höchste Anforderungen und bietet optimale Ergebnisse. So entsteht mittels Einspritzdruck, Werkzeug, Abkühlungsprozess und Entformung Produkte, die sich in Funktion, Konstruktion, Design und Oberfläche detailgetreu abbilden. Mit dem Spritzgussverfahren können eine Vielzahl von Kunststoff Spritzguss Produkten hergestellt werden. Dazu gehören Verpackungen, technische Bauteile für den Maschinenbau, Gehäuseteile für elektronische Geräte wie zum Beispiel Haushaltsgeräte, Komponenten für Möbel und Fahrzeugbau wie zum Beispiel in Caravans sowie spezialisierte Produkte für die Medizintechnik.
Spritzguss Fertigungsverfahren Überblick
Auf dieser Seite finden Sie weiterführende Informationen zu:
- Fertigungsschritte im Detail
- Vorteile Spritzguss
- Spritzgussteile Vielfalt
- Arten Spritzgussprodukte
- Gestaltungsrichtlinien im Spritzguss
- Konstruktionsregeln
- Spritzgusswerkzeug
- Hinterschneidungen
- Wandstärke
- Einfallstellen
- 2k Spritzguss
- Bindenahtfreies Spritzgießen
- Hybridbauteile
- Inmould-Verfahren
- Zusammenfassung Spritzgießen
Produktion Spritzguss
Fertigungsschritte im Detail
- Granulatvorbereitung: Das Rohmaterial wird wenn nötig getrocknet und für die Verarbeitung vorbereitet
- Plastifizieren: Das Kunststoffgranulat wird in der Spritzeinheit durch Hitze und Reibung aufgeschmolzen.
- Einspritzen: Die Schmelze wird in die Form eingespritzt.
- Kühlen und Erstarren: Der Kunststoff kühlt in der Form ab und nimmt seine endgültige Gestalt an. Über den Nachdruck wird während dieser Phase kontinuierlich Material weiter langsam eingespritzt, um die Schwindung zu kompensieren.
- Entformen: Das fertige Teil wird aus der Form entnommen.
- Folgeprozesse: Je nach Produkt erfolgen Folgeprozesse, z. B. Inline-Montage oder das Bedrucken.
Spritzgussverfahren Vorteile
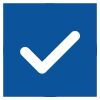
Hohe Produktionsgeschwindigkeit
Spritzguss ermöglicht die Herstellung großer Stückzahlen in kurzer Zeit und ist daher für die Massenproduktion besonders geeignet.
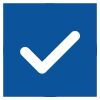
Präzision
Komplexe und feinste Strukturen können mit hoher Genauigkeit hergestellt werden.
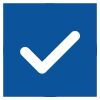
Materialvielfalt
Es können unterschiedlichste Kunststoffe, inklusive hochleistungsfähiger und biobasierter Kunststoffe, verarbeitet werden.
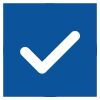
Vielseitigkeit
Das Verfahren eignet sich sowohl für großformatige als auch für mikroskopisch kleine Bauteile.
Spritzgussteile Vielfalt & Präzision
Spritzgussteile ermöglicht die präzise und reproduzierbare Herstellung komplexer Kunststoffprodukte in großen Stückzahlen – mit hoher Maßhaltigkeit, kurzen Zykluszeiten und breitem Materialspektrum. Die Anwendungsbreite der Spritzgussteile ist enorm.
- Verpackungen, z. B. PET-Flaschen, Verschlusskappen, Becher
- Funktionsteile und technische Bauteile, z. B. Gehäuse, Befestigungselemente, Clips, Dichtungen oder Lagerkäfige
- Sichtteile mit hohen Anforderungen an Oberfläche und Design, z. B. Blenden, Bedienfelder oder Zierabdeckungen
- Strukturelle Bauteile, wie Halterungen, Stege, Verstärkungen oder Verbindungselemente
- Mikroteile für die Medizintechnik oder Elektronik
- Mehrkomponentenbauteile (2K-/3K-Spritzguss) zur Kombination unterschiedlicher Materialien in einem Fertigungsschritt
- Hybridteile, bei denen Kunststoffe mit Einlegeteilen aus Metall, Glas oder anderen Werkstoffen kombiniert werden
Welche Arten von Spritzgussprodukten gibt es?
Die Bandbreite der Spritzgussprodukte richtet sich nach dem Anwendungszweck, den Anforderungen und dem eingesetzten Werkstoff. Grundsätzlich unterscheidet man:
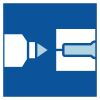
Technische Spritzgussprodukte
Mechanisch beanspruchbare Funktionsteile mit hohen Anforderungen an Maßhaltigkeit, Stabilität oder Medienbeständigkeit.
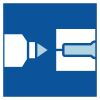
Optische Spritzgussprodukte
Teile mit Fokus auf Ästhetik und Oberflächenqualität, z. B. für Konsumgüter oder Fahrzeuginterieur.
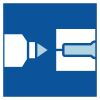
Spezialbauteile
Z. B. transparente Komponenten, Weich-/Hart-Kombinationen oder elektrostatisch ableitfähige Teile.
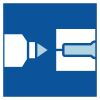
Kundenspezifische Sonderlösungen
Komplexe Formteile nach Maß, entwickelt und gefertigt nach individuellen Anforderungen.
Gestaltungsrichtlinien im Spritzguss
Die Einhaltung der Konstruktionsregeln im Spritzguss entscheidet maßgeblich über die Bauteilqualität, Werkzeuglebensdauer und Wirtschaftlichkeit. Ich unterstütze Sie dabei, diese Regeln gezielt umzusetzen – für Bauteile, die im Werkzeug, im Prozess und in der Anwendung überzeugen. Wer die Gestaltungsrichtlinien für den Spritzguss kennt und konsequent anwendet, verhindert Fehler frühzeitig – und spart im späteren Prozess Zeit und Kosten.
Die Konstruktion von Spritzgussteilen folgt eigenen Regeln. Das Kunststoffformteil muss nicht nur „funktionieren“, sondern auch form- und entformbar, verzugfrei, materialeffizient und werkzeuggerecht sein.
Konstruktionsregeln im Überblick
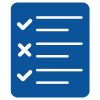
Gleichmäßige Wandstärken
Unregelmäßige Wanddicken führen zu Einfallstellen, Spannungen und Verzug. Das Ziel ist daher immer eine möglichst gleichmäßige Materialverteilung im Bauteil.
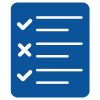
Vermeidung von Massivstellen
Dicke Materialanhäufungen kühlen langsam aus – mit hoher Gefahr für Lunker und Einfallstellen. Die Lösung liegt in der Versteifung durch Rippen statt Materialvolumen.
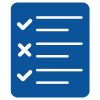
Ausreichende Entformungsschrägen
Flächen senkrecht zur Entformungsrichtung müssen mit einem Auszugswinkel von mindestens 0,5–1,0° (besser mehr) versehen werden, um Schäden beim Auswerfen zu vermeiden.
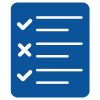
Radien statt scharfer Kanten
Innen- und Außenkanten sollten abgerundet werden. Das ermöglicht eine bessere Füllung und bedeutet eine geringere Spannungskonzentration sowie eine längere Werkzeuglebensdauer.
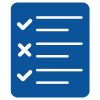
Funktionsgeometrien werkzeuggerecht gestalten
Schnapphaken, Rastnasen oder Durchbrüche müssen entformbar sein, wenn möglich ohne aufwändige Schieber. Hinterschneidungen können nicht immer vermieden werden. Wichtig ist, in Bezug auf die Werkzeuglebensdauer immer die beste Lösung zu finden.
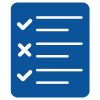
Anguss- und Entlüftungszonen berücksichtigen
Die Konstruktion muss den Fließweg, die Anspritzung und die Entlüftung des Werkzeugs mitdenken – nur so ist eine vollständige und fehlerfreie Füllung gewährleistet. Bei der Anspritzung ist der Heißkanal ist ein wichtiger Werkzeugbestandteil, der entsprechend sorgfältig ausgewählt werden muss. Je nach Projekt müssen Heißkanäle jedoch auch bewusst vermieden werden.
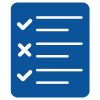
Werkstoffgerechte Gestaltung
Die Bauteile müssen so ausgelegt werden, dass sie Belastungen, Wärmedehnung oder Umwelteinflüsse standhalten.
Spritzgusswerkzeug Konstruktion
Die Konstruktion des Spritzgusswerkzeugs ist entscheidend für die Qualität des Endprodukts. Nur wenn das Werkzeug präzise gefertigt wurde, sind die produzierten Teile maßgenau und weisen ein sauberes Oberflächenfinish auf.
Jedes Spritzgusswerkzeug wird dabei speziell nach den jeweiligen Anforderungen individuell in Bezug auf Material, Formgebung und Funktionalität entwickelt. Je nach Anwendung können zusätzliche Funktionen wie Einlegeteile, Label oder Montage im Werkzeug integriert werden.
Das Spritzgusswerkzeug, das für die Serienfertigung der Kunststoffteile benötigt wird, ist eine Form, die meistens aus zwei Hälften besteht. Wenn die beiden Werkzeughälften geschlossen sind, spritzt die Spritzgießmaschine den geschmolzenen Kunststoff in die Form. Nach dem Abkühlvorgang wird das Werkzeug geöffnet und Kunststoffteil ausgeworfen.
Spritzgusswerkzeug
Das Spritzgusswerkzeug ist das Herzstück jedes Spritzgießprozesses. Es bestimmt nicht nur die Form und Funktion des späteren Kunststoffteils, sondern auch entscheidend die Qualität, Zykluszeit und Wirtschaftlichkeit der Produktion. Umso wichtiger ist eine anwendungsgerechte Auslegung, hochwertige Konstruktion und sorgfältige Herstellung des Werkzeugs.
Ein klassisches Spritzgusswerkzeug besteht aus zwei Haupthälften – der Düsenseite (Festseite) und der Auswerferseite (Bewegungsseite). Vor dem Einspritzen wird das Werkzeug geschlossen, die Schmelze in die Kavität eingespritzt und nach dem Erstarren das Bauteil durch Auswerfer oder Kernzüge entnommen.
Weitere Elemente, die je nach Komplexität zum Einsatz kommen können:
- Kühlkanäle für kontrolliertes Temperaturmanagement
- Heißkanalsysteme zur materialeffizienten Verarbeitung ohne Angussreste
- Schieber, Kernzüge oder Gewindekerne für Hinterschnitte oder Innengewinde
- Multikavitäten zur parallelen Herstellung mehrerer Bauteile pro Zyklus
Je nach Anwendung, Losgröße und Geometrie unterscheidet man unter anderem zwischen folgenden Werkzeugarten:
- Prototypenwerkzeuge – aus Aluminium oder gehärtetem Stahl, für erste Muster und Vorserien
- Serienwerkzeuge – meist aus gehärtetem Stahl, ausgelegt für hohe Stückzahlen und Dauerbelastung
- Wechselwerkzeuge – modulare Werkzeuge mit austauschbaren Einsätzen für Variantenfertigung
- 2K-/3K-Werkzeuge – für Mehrkomponentenbauteile, mit Drehteller oder Schiebetechnik
- Familienwerkzeuge – zur Herstellung mehrerer Geometrievarianten in einem Schuss
Das sind die Anforderungen an ein leistungsfähiges Spritzgusswerkzeug:
- Maßhaltigkeit und Passgenauigkeit: für prozesssichere Produktion und enge Toleranzen
- Zuverlässige Entformung: über Entformungsschrägen, Auswerferstifte oder komplexe Mechanik
- Optimierte Zykluszeit: durch intelligente Kühlkanalführung und präzises Temperaturmanagement
- Wartungsfreundlichkeit: modulare Bauweise und leichte Zugänglichkeit von Verschleißteilen
- Langlebigkeit: durch korrosionsbeständige Stähle, Hartbeschichtungen und präzise Fertigung
Ein optimal ausgelegtes Werkzeug sorgt für kurze Taktzeiten, stabile Serienprozesse, eine hohe Wiederholgenauigkeit, geringe Nachbearbeitungskosten, einen minimierten Ausschuss sowie geringe Ausfallzeiten. Gerade bei technisch anspruchsvollen Kunststoffteilen lohnt sich die Investition in ein professionell konzipiertes Werkzeug. Denn: Je komplexer das Teil, desto entscheidender ist die Werkzeugtechnik für den späteren Fertigungserfolg.
Hinterschneidungen im Spritzguss
Der Begriff Hinterschneidung beschreibt im Spritzgussbereich Geometrien an einem Bauteil, die sich nicht in direkter Entformungsrichtung auswerfen lassen – sie „klemmen“ sozusagen im Werkzeug. Eine Hinterschneidung im Spritzguss stellt daher eine besondere konstruktive und werkzeugtechnische Herausforderung dar. Typische Beispiele für Hinterschneidungen sind Rastnasen und Haken, seitliche Durchbrüche, Schnappverbindungen, umlaufende Sicken oder Nuten und Einclips-Geometrien.
Technisch sind Hinterschneidungen kein Problem – wenn man sie richtig einplant. Mithilfe von Schiebern, Kernzügen oder flexiblen Entformungslösungen lassen sich viele Hinterschneidungen problemlos realisieren. Die Voraussetzung: Die Konstruktion muss dies frühzeitig berücksichtigen, damit das Werkzeug entsprechend aufgebaut werden kann.
Was bei der Konstruktion zu beachten ist:
• Hinterschneidungen möglichst funktional begründen – z. B. für Montage, Arretierung oder Design
• Entformbarkeit simulieren oder prüfen
• Bei flexiblen Kunststoffen: elastische Entformung (Durchbiegung) in Betracht ziehen
• Werkzeugtechnik (Schieber, Formkerne, Abstreifer) bereits in der Entwicklungsphase des Kunststoffteils berücksichtigen
Hinterschneidungen im Spritzguss bieten viele gestalterische Möglichkeiten, erfordern aber ein durchdachtes Zusammenspiel von Konstruktion, Werkstoffwahl und Werkzeugtechnik. Ich unterstütze Sie dabei, auch komplexe Geometrien wirtschaftlich und prozesssicher umzusetzen – mit Erfahrung, Simulation und einem Gespür für das Machbare.
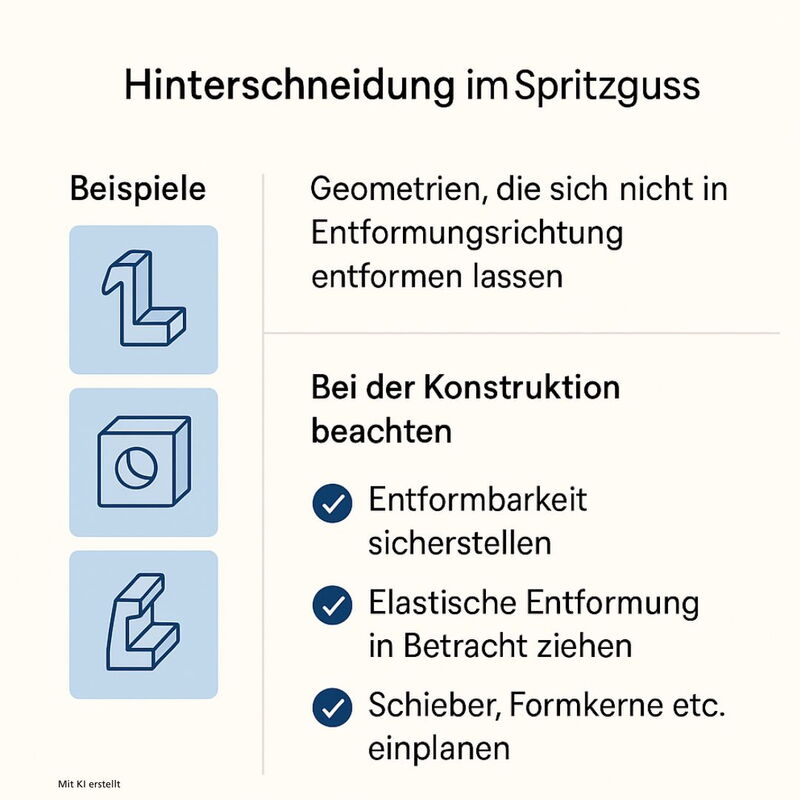